Phil Clifford on the importance of robust record keeping when it comes to vehicle maintenance.
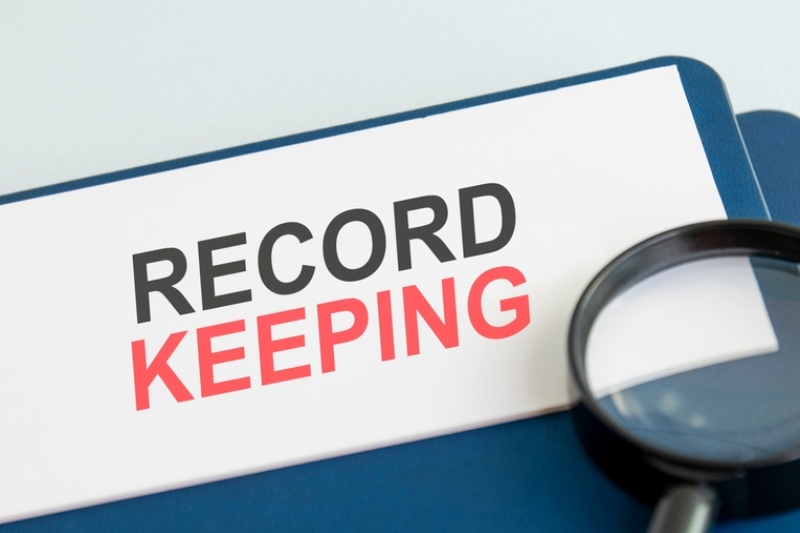
During my career in local government I only once had the experience of being questioned by a DVSA enforcement officer. I wasn’t initially worried on being told he would be calling in for a discussion and to interview me and my team – why would I be? I was confident that my systems were up-to-date and that records would be deemed to be robust.
To cut a long story short, I was given a near clean bill of health but not without having received some advice that I hadn’t expected. The experience made me think about the whole process of record keeping and how it is essential to ensure that complacency doesn’t creep in.
One of my current tasks is to carry out independent compliance audits for fleets and my role has the benefit of being a professional ‘devils-advocate’. With all records it is possible to be critical but I have been amazed at how many ‘silly’ mistakes creep in to maintenance records which, without proper management, can develop into a major issue that would not stand the scrutiny of the DVSA.
Many operators have the benefit of computerised maintenance records, whether these be generated in-house or from an external maintenance provider. A large proportion, however, still rely on pre-printed inspection forms which are completed manually by a technician.
One common error I have found is that where an operator undertakes their own inspections, using such pre-printed stationary, the identity of the workshop carrying out the repairs is not clearly identified. Third party workshops would normally (although not always!) apply their dealer stamp to the sheet when completed but I find that in-house operations often do not. They probably think it is obvious who has carried out the maintenance but, at a future inspection of records, it may not be obvious to the auditor concerned, especially if the operator uses a mixture of in-house and out-sourced provision.
Other common errors which often creep in are:
• Using out-of-date inspection sheets – compare them regularly with the requirements of the ‘Heavy goods vehicle (HGV) inspection manual’;
• poor handwriting which can be ambiguous;
• incorrect odometer readings – miles or kilometres: decide which it should be and stick to it;
• date of inspection – this should be the date the inspection is carried out and NOT the date it, and any remedial works, were completed;
• date the tachograph is due for calibration;
• all inspection items have been endorsed with either a ‘tick’ for serviceable, an ‘x’ for not serviceable, and ‘n/a’ for items not applicable to the vehicle type;
• signature and printed name of the technician undertaking the inspection followed by a counter signature from a senior technician/workshop manager to confirm a quality check has been undertaken;
• cross reference to any driver defect reports that have been submitted ensuring no defects are overlooked;
• brake test readings, preferably with a separate brake test report sheet, clearly indicating if laden or unladen and ensuring that someone has renewed the ink ribbon in the printer, so the sheet is legible;
• full list of defects found on inspection indicating what action has been taken for each with, as appropriate, the inspection manual number to identify the fault with the tick list.
This list is not exhaustive, but I am sure you get the picture that clear and concise records will serve you well should the DVSA ever scrutinise your operation.
The most important factor is to ensure that the inspections are carried out at the correct intervals. Depending on your reasoned choice of interval, ensure that all inspections fall within those periods and that any variances, for whatever reason, are well documented with a file note ensuring that no gaps exist which may be construed as a late or missed inspection. Finally, ensure that all records are kept and filed securely for at least 15 months.
I believe most operators are working towards electronic records through data capture devices, but it is still essential that technicians are trained fully to ensure that the whole process does not fall victim to the ‘tick-box’ syndrome and that it remains meaningful. Fleet maintenance should be given the attention that it not only deserves but is expected by the traffic commissioner.
This article originally appeared in the spring 2022 issue of LAPV. Sign up here to get your free copy of the magazine.