Workshop equipment experts Totalkare make the case for why local authority workshops should invest in a tyre changer. LAPV reports.
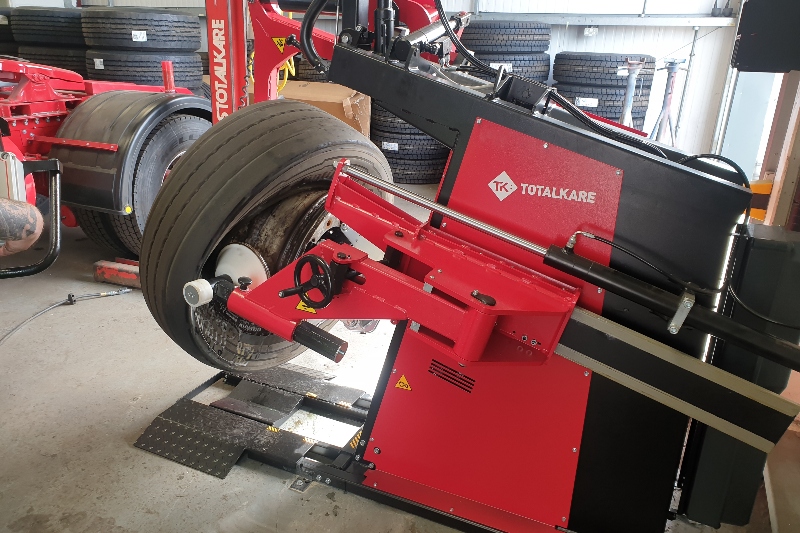
Let’s be honest: changing tyres isn’t an everyday job. In most cases, it takes years on the road (or tens of thousands of miles) before your vans and coaches need a new set of treads. But when we’re talking about scale – fleets with dozens of commercial vehicles, or busy workshops with high demand – things start to get serious.
That’s when a dedicated tyre changer can save you serious time and money.
1. Tyre changers save time
Changing a tyre is a heavy-duty job, but that doesn’t mean it’s a slow and laborious one. The technology behind tyre changers has come a long way in the last few decades, with newer pieces of kit that are safer, easier, and faster to handle.
Our own NAV101 Tyre Changer, for example, can remove and replace a tyre in just 30 seconds.
That’s faster than the phone call to book a third-party engineer – never mind the wait for an actual visit.
With the right in-house equipment – and the right training for your staff – a single dedicated tyre changer can replace the tyres of an entire small fleet in less than a day. And you won’t be at the mercy of your contractor’s schedule.
2. Tyre changers save you money
We’d be lying if we said a tyre changer was a cheap piece of kit. But that upfront investment comes with its own savings, especially when you look at the long term.
When you outsource your tyre changing to a third-party service, you’re paying their fees. You’re paying for the fuel on the journey to their site, and you’re paying for the extra wear and tear on your vehicles over that distance. You’re also paying one of your team for the time it takes to drive to the service – and that means you’re missing out on revenue that they could be earning doing other jobs.
Of course, we wouldn’t recommend an in-house tyre changer for a business with one or two vehicles in their fleet. But if you’re dealing with dozens of vehicles – whether that’s your own fleet or the vehicles that visit your workshop – all of those costs can start to add up. If you compare those costs to the price of an in-house tyre changer, you might be surprised at how much you could save.
3. Tyre changers are safer than ever
Even the smallest commercial tyres carry some serious weight. And the forces involved in changing a tyre can be huge. But these days, in-house technology is more advanced than ever – and we’re proud to say that Totalkare equipment is some of the safest gear available today.
All of our Totalkare Tyre Changers work with a hands-off operation, with controls on a separate console to keep your staff at a safe distance from the motion of the wheel. Models like the NAV11 Tyre Changer (a model that’s built to handle heavy-duty vehicle wheels) can give your teams complete control over the speed of the carriage, helping them to stay safe and work at their own pace. Our smaller NAV26HW can even be used safely on roadside services.
4. In-house tyre changers make compliance easy
Commercial vehicles come with plenty of red tape – and your wheels and tyres are no different. You need to be sure your entire fleet is safe and roadworthy, with regular inspections and services to stay compliant and legal. And with frequent check-ups and tests, it won’t always make sense to keep contracting those jobs out to third-party companies.
But with an in-house tyre changer, you’ve got a service on tap on your own premises – ready and available for every last-minute inspection, unexpected delay, or damage to your vehicles that need to get back on the road.
Ready to take control of your vehicle servicing?
If you’re running a big fleet or your workshop’s in demand, every outsourced job can start to add up – in terms of both time and money. That’s why more and more vehicle-based businesses are bringing their testing and servicing in-house, investing in their own dedicated equipment that’s reliable, safe, cost-effective, and always available.
So if you’re looking to scale up your operations (and save some time and money along the way), check out our full range of in-house equipment or chat to one of our experts and we’ll guide you through your options.
This article first appeared in the autumn issue of LAPV. To subscribe for free click here.